Wireless Signal Transmission with RTM MP
Are you looking for a telemetry system that does not require slip rings? And, is the parallel transmission of different types of signals for universal applications important to you? Then an easy-to-retrofit and quick-mount RTM MP from FMS could be the answer.
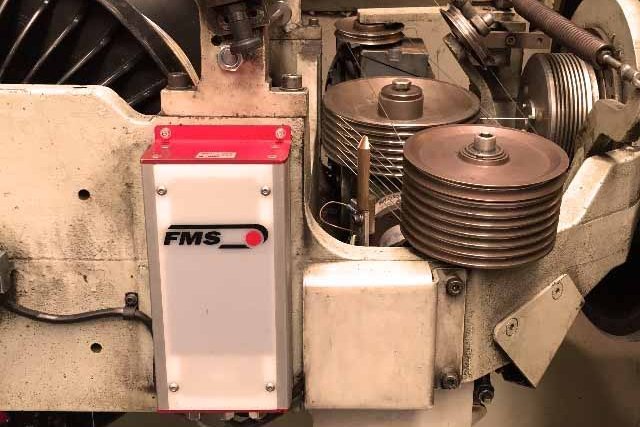
Your advantages
- Easy retrofitting without additional slip rings
- Reliable wireless transmission for maximum process reliability
- Robust and maintenance-free
- Parallel transmission in both directions
Properties
- Simple system setup and quick installation
- Proven technologies
- Encapsulated components and insensitive power supply for long MTBF (Mean Time Before Failure)
- Signals: Encoders, digital, analog, force sensors
Our promise
- Reliability
- Long service life
- Maintenance-free operation
- Lowest life cycle costs
Bidirectional, radio-based signal transmission. For rotating machines.
The RTM MP telemetry systemis able to transmit several signals in parallel:
- 2 encoder signals
- 8 digital signals
- 1 analog signal
- 2 force sensors
The RTM MP system is used wherever signal transmission using slip rings reaches its limits. This results in considerable costs for the mechanical adjustments in the case of a subsequent retrofit or extension of a machine with slip rings.
Avoid high costs
Retrofitting or extending a machine with slip rings can result in considerable costs for mechanical adjustments. Many RTM MP systems are used today where a repair of slip ring carriers is not possible. Be it due to high retrofit and spare parts costs or because no spare parts are available for older existing machines. Robust components, simple system setup, and maintenance-free operation, as well as easy retrofitting of the compact components have made the RTM MP system especially successful when retrofitting older bow stranders.
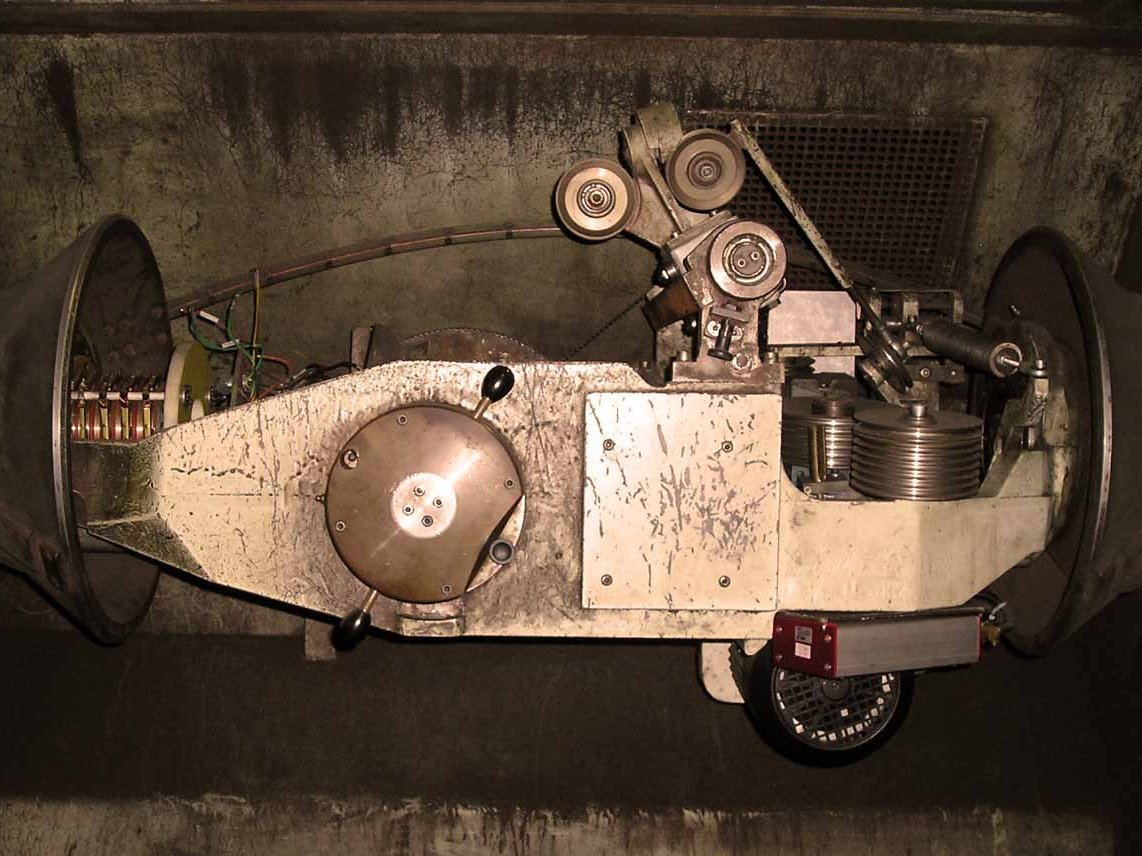
Function description
The RTM MP system consists of only three components. One transceiver in the rotating part of the machine, one at the operator’s stand and also a module for signal decoding at the control panel. The two modules at the operator's stand of the machine are connected to each other via an interface. The signal lines are simply connected to the transceiver in the machine. Communication with the module at the operator's stand is realized in real time via a stable radio link. Another module handles data processing and communication with the PLC or other independent controllers. The processed signals can then be routed back to the machine in the same way. The module in the machine is simply powered by the existing machine power supply.