Are you looking for a force sensor, also known as force transducers or load cells, with a long service life that is maintenance-free? Should it be suitable for your installation and application situation? Does it need to have the highest sensitivity for precise measurements? Then a force sensor from FMS, for your demanding applications, is the right product for you.
Your advantages
- Reliable, proven technology
- Precise measurement results
- For every installation and application situation
- Options for the most demanding applications
Properties
- Strain gauge in full-bridge circuit to compensate for temperature influences
- Measuring body and housing made of stainless steel or high-strength aluminum, mechanical overload protection, robust with high repeatability
- Different series, sizes and nominal forces for a wide range of web tensions
- For elevated temperatures, aggressive environments, special installation conditions, vacuum applications
Our promise
- Highest precision above the market standard
- High reliability and long service life
- Only supplier of double range measuring bearing
- Wide range of constructive solutions
- 100% compatible
- Custom-made products possible
The FMS force sensors. A success story.
FMS has been producing force sensors for the industry for more than 30 years. FMS has succeeded in creating a unique portfolio with innovative developments. Due to their long service life and their sophisticated design, they have a become a reputable product.
Continuously optimized
Due to continuous improvements and continuous maintenance and extension of their portfolio, FMS force sensors offer maximum performance and efficiency for end customers as well as for OEMs.
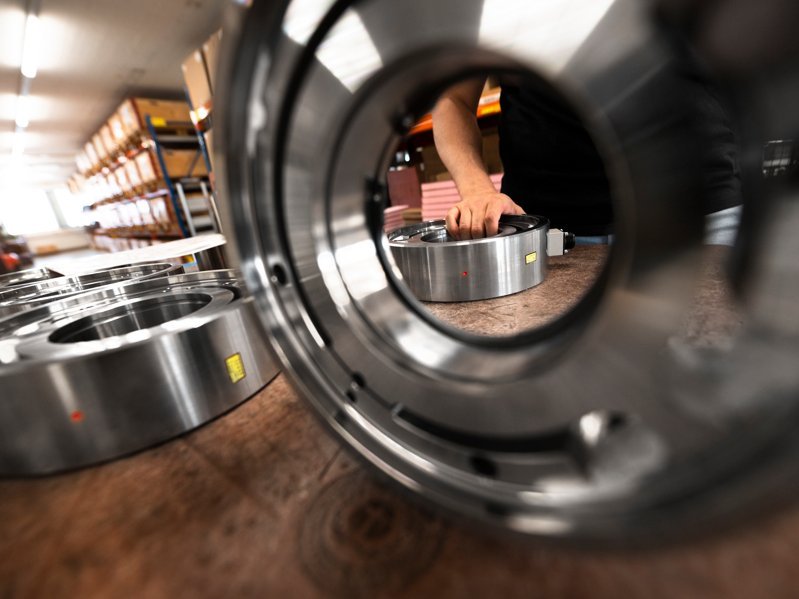
Meeting requirements
The proven principles of the FMS design such as double bending beams and the use of strain gauges (SG) in full-bridge circuits and the integrated overload protection help us to always meet the expected requirements.
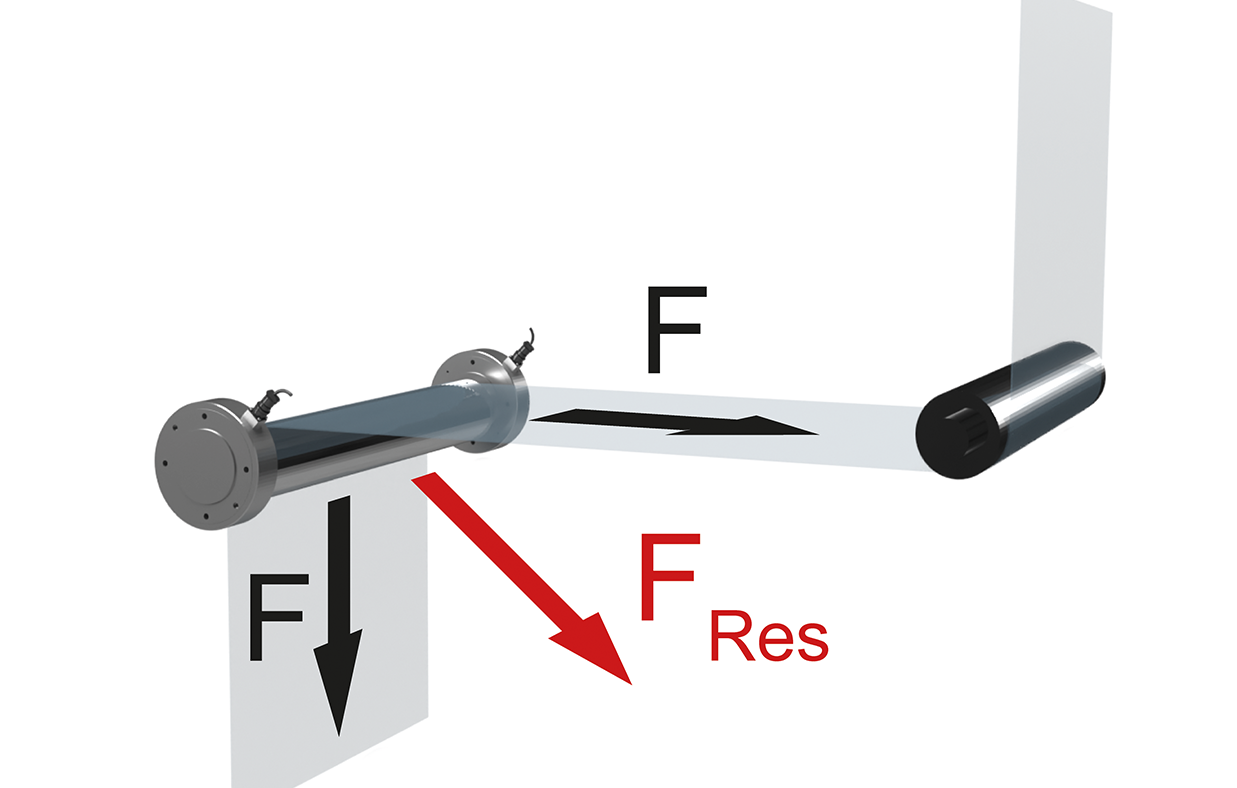
Function description
Our force sensors are supplied with a highly stable voltage (typically 5 VDC) from the measuring amplifier. When the force sensor is loaded, the strain gauges are compressed or stretched. This change in length causes a change in the resistance value of the full bridge circuit. The output signal (in the mV range) of the force sensor goes back to the amplifier. There, this change is registered and further processed so that the user can read a force value at the end. The great advantage of the strain gauge full bridge circuit is its simple and robust design. Temperature changes of the environment are almost completely compensated by this arrangement. The integrated, mechanical overload protection prevents damage to the force transducer, even in the case of unforeseeable overloads, thus contributing to longevity and precise measurement results. All products in the FMS web tension measurement range can be freely combined with each other, allowing you to put together the best possible solution for your application.
Questions and answers
What is a force sensor?
Force sensors are used to measure compression, force, strain and load. Many have internal strain gauges bonded to the metal structure which react to even the smallest deformation causing a change in resistance and giving feedback on these results. Force sensor is an alternative term used for a load cell, force transducer or force measuring bearing.
Where are force sensors used?
One of the most common uses is for tension control applications. Web type material is fed over an idler roller. Force sensors on each end of this roller detect the force that acts on the roller generated by the material tension. The feedback signal from the force sensors is processed and delivers a direct indication of the strain or tension in the material in Newtons, kilograms, grams or pounds. Applications for wire tension control apply a pulley/sheave and a single force sensor instead of the roller with two force sensors.
What is the difference between dead shaft and live rollers?
Dead shaft rollers are usually made of two separate parts. The non-rotating axis and the roller sleeve are connected via bearings. This allows the sleeve to rotate around the axis. In contrast, live shaft rollers are made from one piece. A bearing sits in force sensors on either end of the roller. Dedicated types of force sensors are available for both types of rollers.