Fit for future in only four days
How does a virtually indestructible basket style stranding machine, type Krupp “KVR 8x1400” with reverse twist, manage to be upgraded to meet future process requirements with the shortest possible downtime of only a few days? The project team of Acoteq GmbH employees are now able to provide their thoughts here from lessons learned during the upgrade process.
The first step was to define the requirement specifications together with the end customer. For the modernization of a Krupp stranding machine "KVR 8x1400" with reverse rotation (year of manufacture 1977), the following customer requirements had to be met: Operator settings should be simplified and shortened by the use of recipes. The current tension should be measured before the stranding point and the tension from full to empty spools should be kept constant by an automatic tension control method during production runs. It was also desired that all measured parameters be recorded and archived, and that the pneumatically actuated spool brakes be replaced. For individual control, a disk brake system had to be installed and the machine must stop when the tolerance of the limit values (wire tension) is exceeded or not reached. Consistent high quality must be ensured independent of the machine operator. Particular challenges were the integration of the systems into the existing Krupp stranding machine (reverse rotation), and to do this as efficiently as possible. This included development of a mechanism to transfer the linear motion of the “RTM X42” brake actuators to the disc brake systems.
Selection of components
For the selection of components, Acoteq chose FMS Force Measuring Systems from Switzerland. For 15 years, FMS has been the only manufacturer capable of offering a complete range of technologies for force measurement, data processing, and radio transmission of signals in stranding machines. The telemetry system “RTM X42” offers all technical solutions as required by the customer, and consists of the wire tension measuring system, the control center, and the brake system. The FMS brake actuators used here are powered by rechargeable batteries, and thus do not require expensive and maintenance-intensive slip rings to provide the required torque at each individual spool. Data transmission is handled by radio (also with a rechargeable battery/no slip rings) in the 2.44GHz band, and therefore the wiring effort on the rotating side of the machine was kept to a minimum. “Thanks to good preparation, such as the construction of special holders for measuring rollers, on-site assembly could be completed in a time window of four days,” explained Willibert Dautzenberg (CEO) and Stefan Krüttgen (project manager) proudly.
Since acceptance and handover to the customer, all desired features have been made available. The main advantages after the modernization are:
- Reduced setup time and reproduction of critical process parameters during product changeovers through the use of recipes.
- The improved quality and throughput with the constant closed-loop tension regulation of the individual strands.
- Recording and documentation of the production parameters over the course of a complete product run.
In addition to the reproduction and optimization of various production processes, complaints are significantly reduced thanks to verifiable process parameters (PDF file).
Source: Jörg Dambock for http://www.wire-magazine.de/
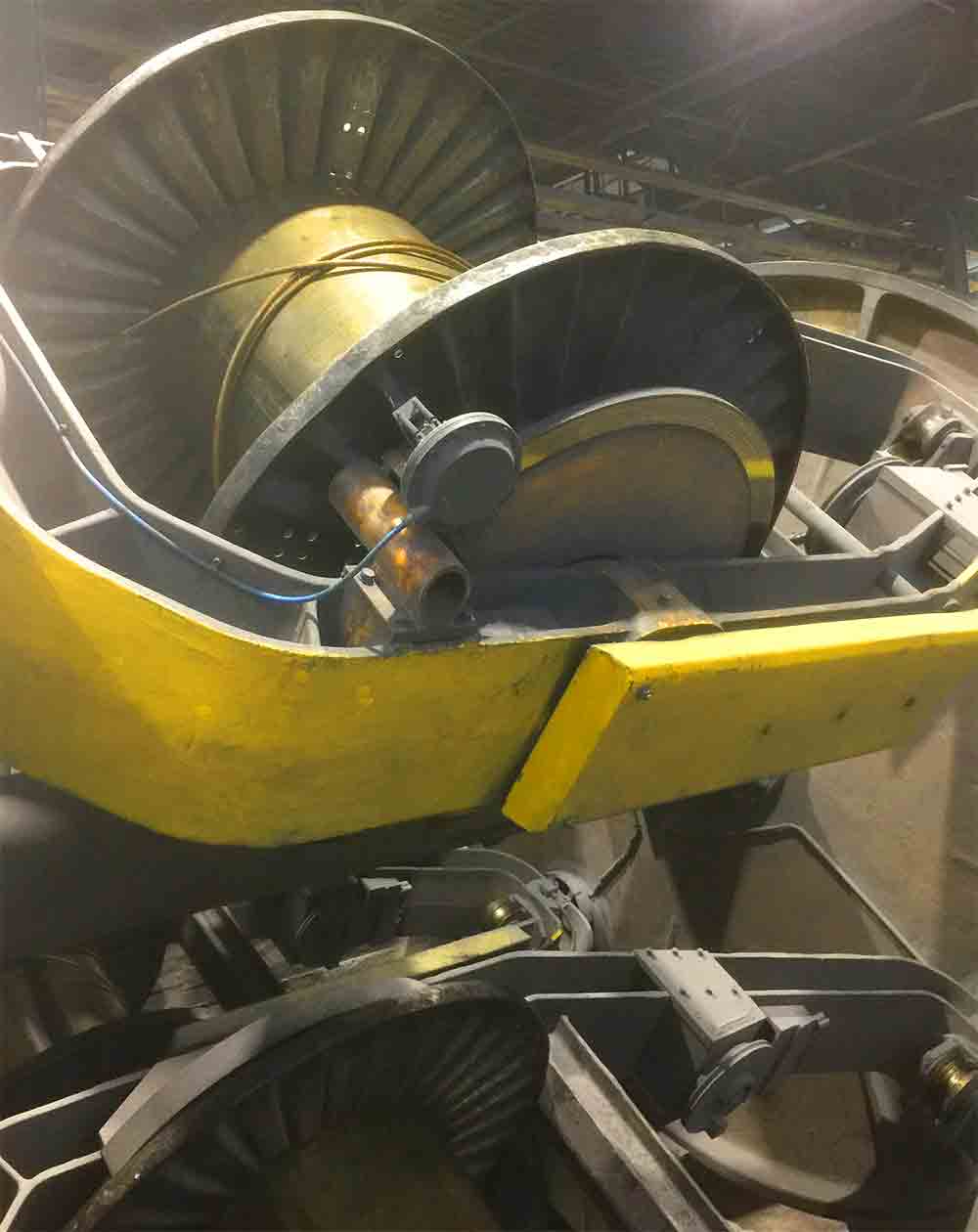
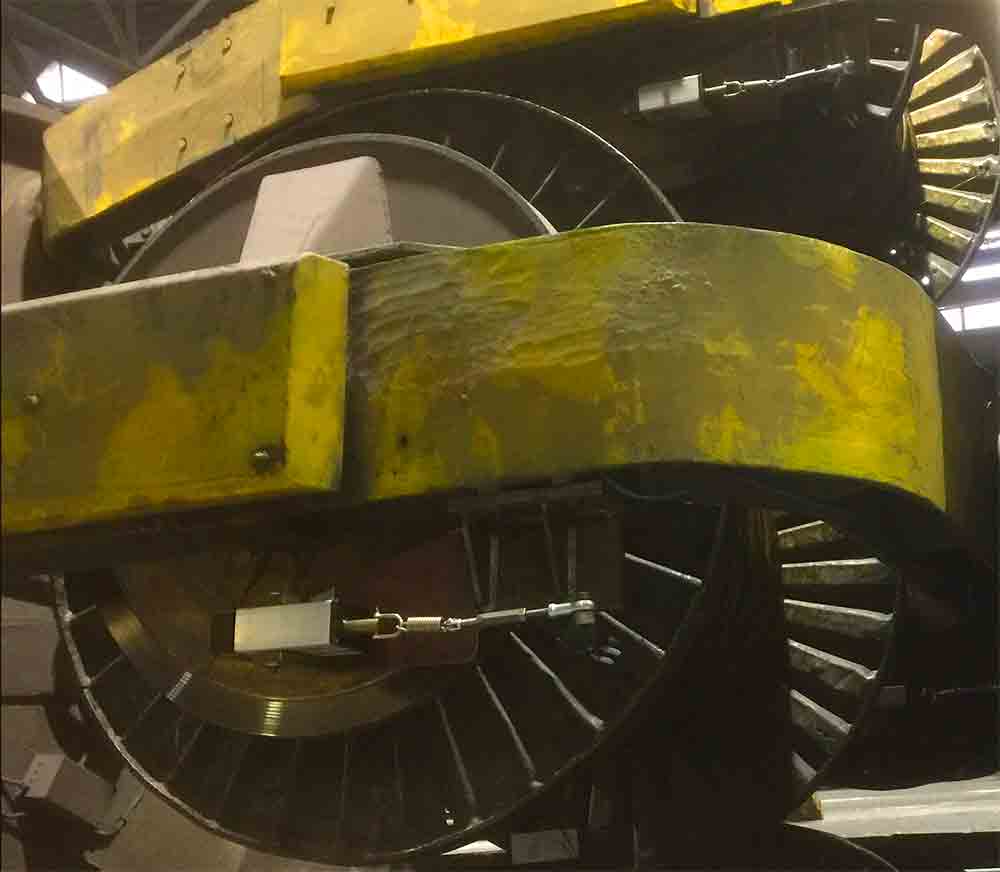