Drop-in replacement for Philips PR9951 at Visy Industries Australia
Global leader for wastepaper recycling selects FMS to supply drop-in replacement for phased-out Philips force measuring blocks.
CGB Precision Products P/L, our Australian partner has recently finalized a retrofit of tension monitoring equipment in Melbourne, Victoria.
When upgrading existing plants, you want to re-use as much components as possible. If these components are no longer produced and spare parts are not available anymore, one needs to search for alternatives. This was the case at the site of the VISY Wastepaper & Waste Management located in Coolaroo, Melbourne.
Planned Upgrade
The actual line has been in operation for 20+ years with regular maintenance and service. However, the key components for web tension monitoring have remained untouched in the past. Due to the planned increase in production speed, a review of the machine design was carried out to assure that all components will meet the desired demands. At this point it became clear that the Philips as the OEM of the tension monitoring equipment no longer exists, and an adequate alternative must be found.
Data Collection
When the responsible engineers of VISY first contacted CGB, the main process and parts data of the installed equipment was noted down. The main goal was to find a suitable replacement for the force measuring blocks with smallest possible modifications to the machine and the PLC. The advantage of the FMS UMGZP-series block is exactly that. A perfect drop-in replacement for the former Philips 9951 block with identical dimensions and even better performance.
Quick Project Realization
After a final check of the resonance frequency, we could confirm the sizing and received the order for the sensors. CGBs proposal to use a dual channel measuring amplifier was highly appreciated. This would allow the operator to monitor the web tension on each side of the web independently. Geving the better insights of the production results, possible faults and adequate counter measures in an early stage of the production process.
Installation and start-up on-site were supervised by the responsible project manager from CGB. After the calibration the machine was back in operation after only a few hours of downtime.
Learn more about the drop-in replacement for the Philips force measuring block PR9951.
How is it done? Calculation of resonance frequency
- All systems, including an idler roller with two force sensors, tend to vibrate at a natural frequency depending upon their mechanical properties. This frequency is known as resonance frequency. When an additional oscillating force from an external source is applied at the same frequency to the roller system, the vibration will cause the roller to oscillate at a higher amplitude (with more force) than when the same force is applied at other, non-resonant frequencies. In roll-to-roll processes the main source for oscillating forces are fast rotating rollers. In the worst case these forces can result in a rocking of the machine with broken bearings, roller or even lead to collapsing frame structures. This must be avoided under all circumstances!
- To assure the highest degree of safety, the first step of FMS is to calculate the resonance frequency of the system. This is calculated in a FEM program based on dimensions and mechanical properties of the roller, including the force sensors. The second step is to compare the resonance frequency of the roller with the oscillation of the machine, based on the rotation speed from material movement and the roller weight. In the best-case scenario, the natural frequency of the roller and the machine vibrations are sufficiently far apart to ensure that the entire machine can be operated completely safely.
Image gallery
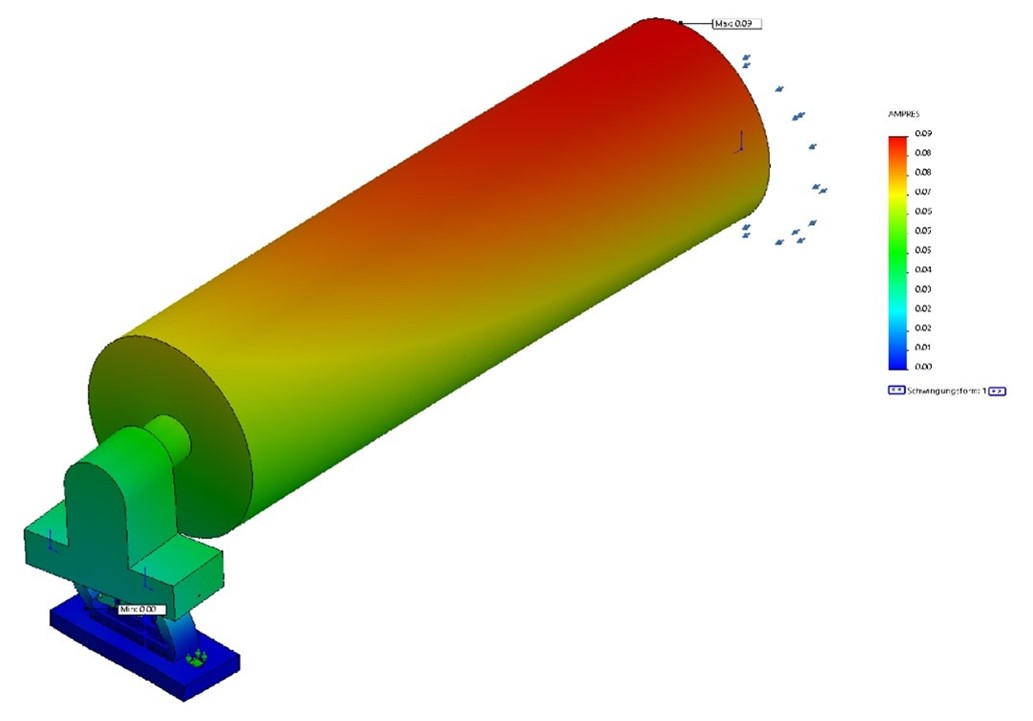
Illustration 1: result of 1st order resonance frequency analysis, deformation is strongly exaggerated
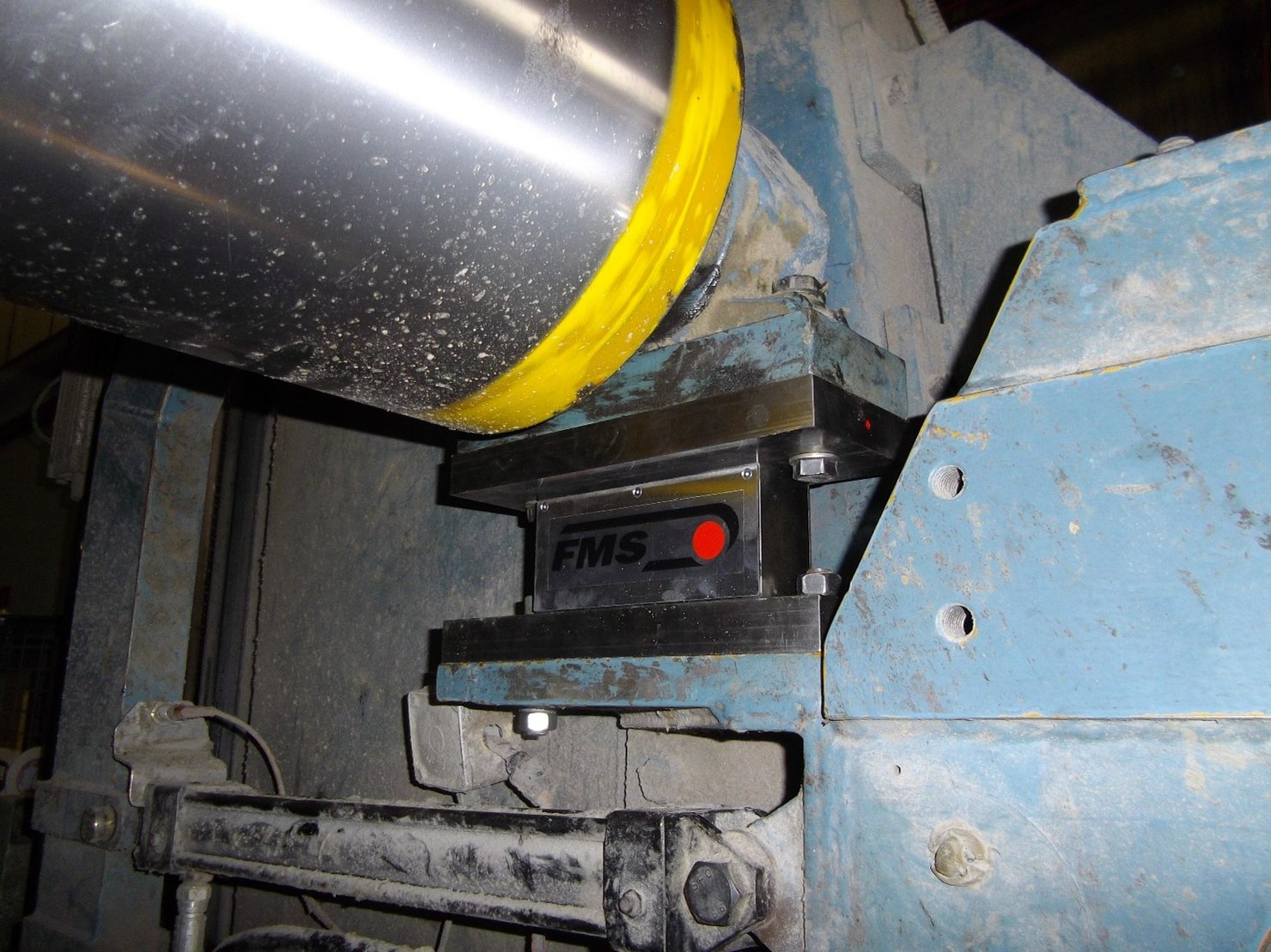
Illustration 2: Installed measuring block of the UMGZP-series
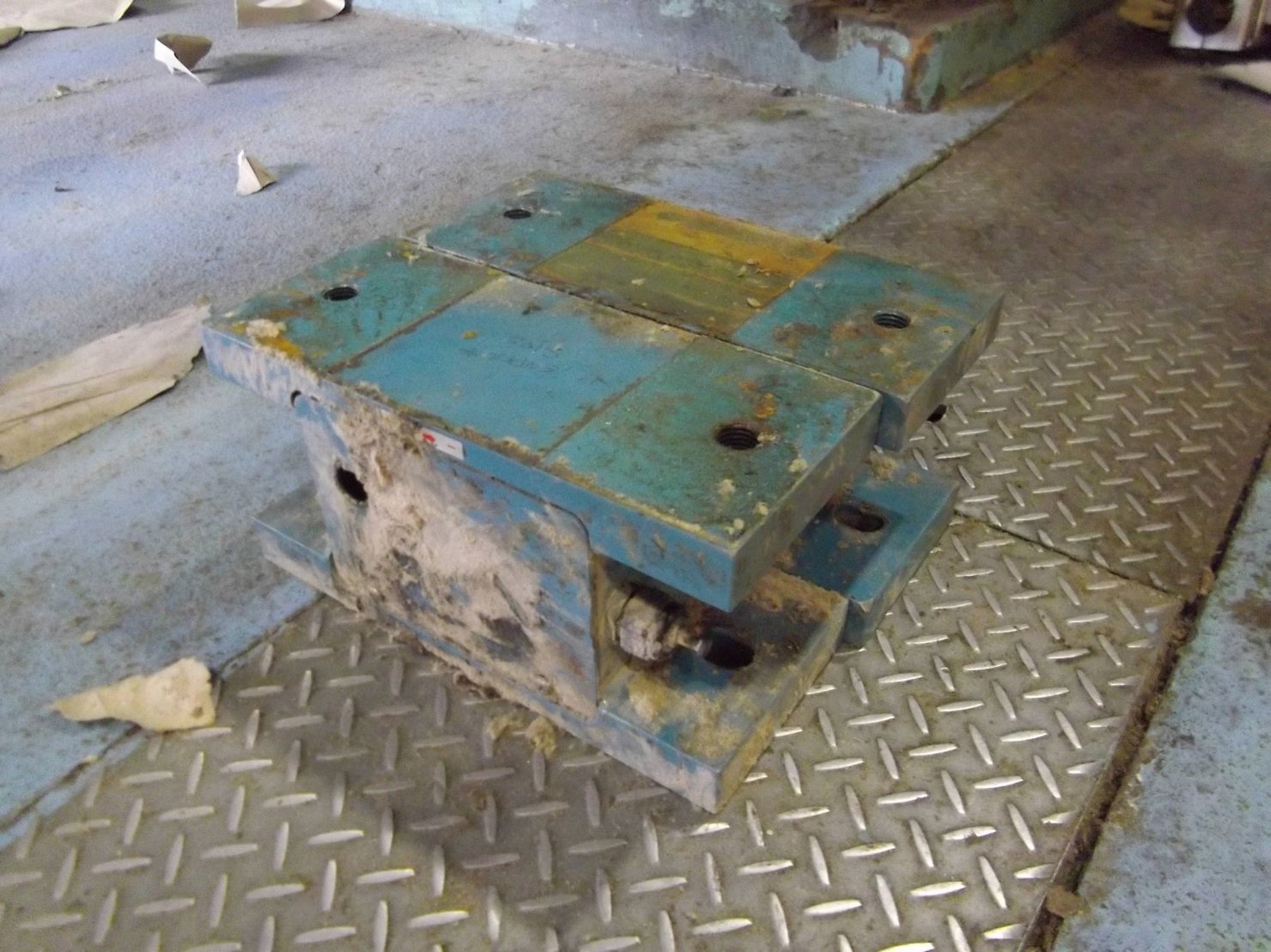
Illustration 3: Philips blocks PR9951, already disassembled
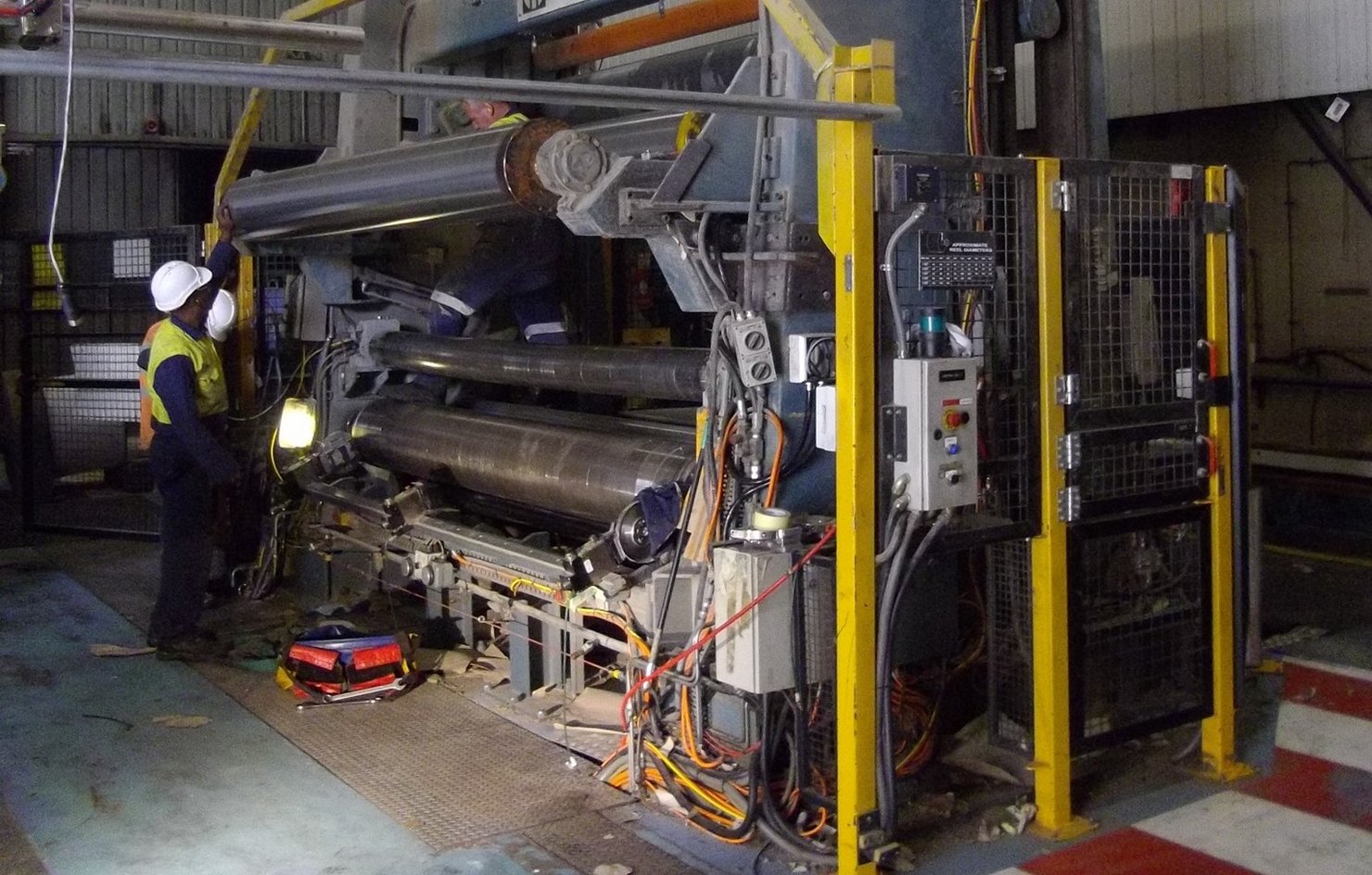
Illustration 4: Winding section with the installed web tension roller during commissioning